Coal Mill Process Ppt
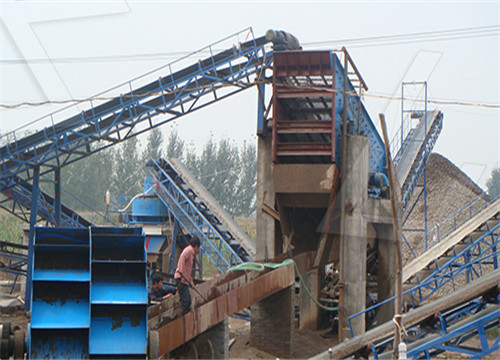
Coal mill pulverizer in thermal power plants SlideShare
2012年11月17日3. 2.Coal pulverizer/mill system One of the critical power plant components that is relied upon to convert the energy stored in coal

PPT PERFORMANCE ANALYSIS OF COAL MILLS
2012年1月23日• The mill grinding heat dissipation, varies from 20 to 40 kJ/kg of coal. Mill Heat Balance: Energy for Drying of Coal • Determine

Coal Mill Part PDF Explosion Chemical Process
高达$3返现Coal Mill Part(3) Free download as Powerpoint Presentation (.ppt / .pptx), PDF File (.pdf), Text File (.txt) or view presentation slides online. Caol mill pat 3. Caol mill pat

Coal Mill In Cement Plant, Air-swept Coal Mill Coal Mill
coal mill parts It mainly consists of a feeding device, main bearing, rotating part, driving device, feeding and discharging device, high-pressure starting device, and lubrication

12.2 Coke Production US EPA
The blended coal mass is heated for 12 to 20 hours for metallurgical coke. Thermal energy from the walls of the coke chamber heats the coal mass by conduction from the sides to

Coal Mill Safety [PPT Powerpoint] VDOCUMENTS
2015年12月22日General Safety Rules Ignition ProcessCoal absorbs oxygen from atmosphereHeat Produced Heat ReleasedTemperature increases and speeds up
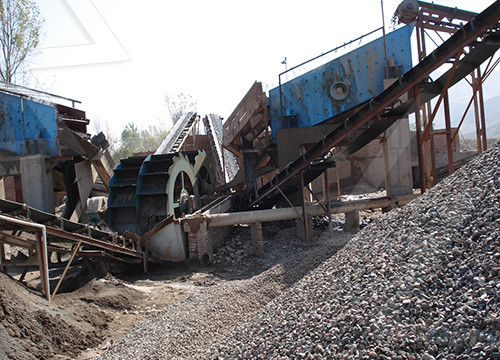
11.25 Clay Processing US EPA
11.25.1 Process Description1-4 Clay is defined as a natural, earthy, fine-grained material, largely of a group of crystalline toothed roll crushers, and hammer mills are used for
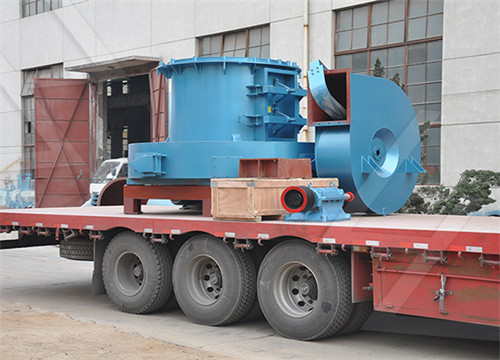
PPT Milling Process PowerPoint presentation free to
The milling process It is known that in the milling process, fat liquors previously introduced in the gaps between fibers are transferred by the mechanical action on to the fibers. 4 Milling process variables
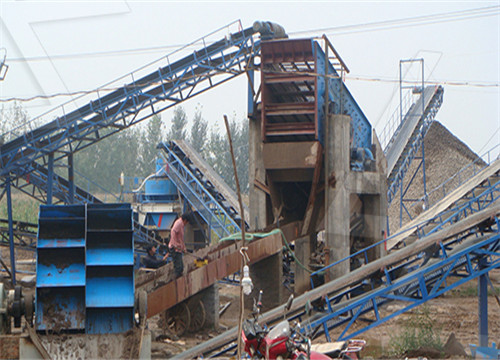
Safety in cement plant SlideShare
2015年6月20日Raw Mill and Preheater Tower: Material in the mill is at temperatures up to 120ºC, in the tower the material can be as hot as 900ºC. Contact with the material is more likely when: Clearing blockages in the
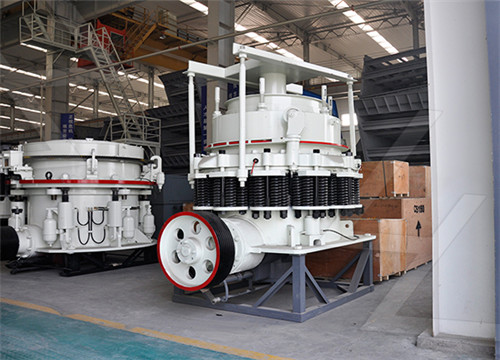
sbm/sbm clinker formation effect in coal mill ppt presentation.md
Contribute to changjiangsx/sbm development by creating an account on GitHub.

Coal Mill Safety [PPT Powerpoint] VDOCUMENTS
2015年12月22日General Safety Rules Ignition ProcessCoal absorbs oxygen from atmosphereHeat Produced Heat ReleasedTemperature increases and speeds up oxidation process (Inside the pile, the heat cannot be released)First three weeks of storage = maximum oxygen intake.Critical Temperature ( 70 80 C) for self-ignition *Coal Shop

Hazards Identification and Risk Assessment in Thermal
In coal crusher coal size reduced up to ¾” after that coal transfer to the boiler’s coal bunker or coal yard. In the case of emergency the coal is fetch from coal yard. Coal feeder control the quantity of coal from coal bunker and send it to the ball mill or roll mill for pulverization process. Where coal crushed to the fine powder
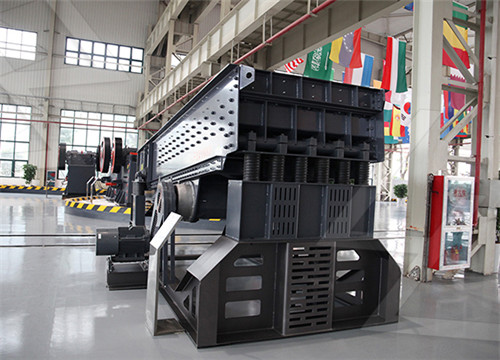
Decarbonization in steel McKinsey
2020年6月3日Steel can be produced via two main processes: either using an integrated blast furnace (BF)/basic oxygen furnace (BOF) or an electric arc furnace (EAF). While integrated players produce steel from iron ore
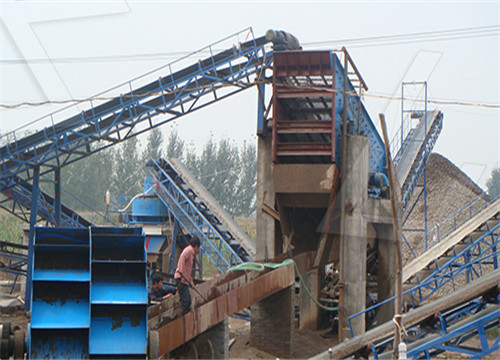
VRM Operation and Optimization PDF Mill (Grinding)
Operation and. Optimization vertical mill used for pre grinding of clinker (lumps to coarse powder) finish grinding (lumps to powder ) of coal/petcoke for kiln raw material for kiln cement, OPC or mixed slag, pure or mixed vertical mills comprise 2-4 conical rollers which are hydraulically pressed onto a horizontal rotating grinding table the roller axis is
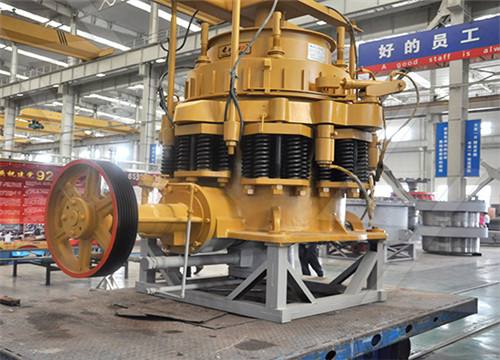
Fire and Explosion Prevention in Coal Pulverizing Systems
Fire and Explosion Prevention in Coal Pulverizing Systems

Flue Gas Desulfurization (FGD) COAL HANDLING PLANTS
2021年4月11日Reagent Preparation System. The reagent preparation system of flue gas desulfurization (FGD) includes a Wet ball mill and cyclone classifiers which produce a finely ground limestone slurry at 90% solids passing through 325 mesh. One mill slurry tank and one slurry pump is supplied for one wet ball mill. The mill slurry pump will send
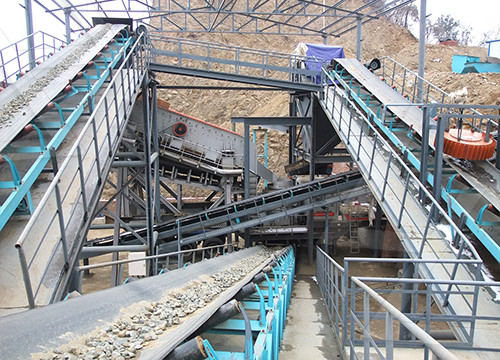
PPT Milling Process PowerPoint presentation
Today the milling drum needs not only to mill, but it is a tool to modify leather. characteristics. 3. The milling process. It is known that in the milling process, fat. liquors previously introduced in the gaps between.
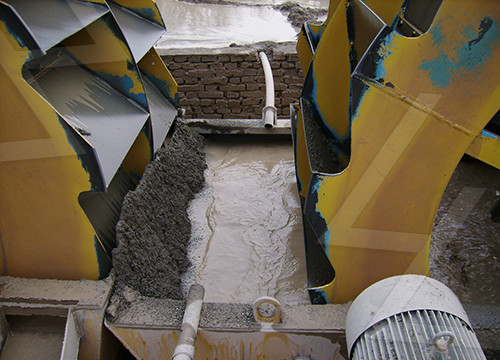
Cement Production Process Cement Manufacturing Process
2020年8月25日Clinker production: The diameter of the clinker ball must between 0.32 and 5.0cm. There are three steps of the high-temperature system: Drying or preheating, calcining, and sintering. The calcining is the core part of the clinker production; the raw meal is weighed and sent into preheater and cement kiln to process clinker.

Energy audit SlideShare
2017年3月12日Energy audit 1. ENERGY AUDIT By- Assi. Prof. SHIVRAJ N NALAWADE Electrical Engineering Dept. NBNSSOE 2. Energy Audit 3. Definition of Energy Audit • As per Indian Energy Conservation Act

BOF and EAF Steels: What are the Differences? Economics 243
2016年3月7日The Electric Arc Furnace The Electric Arc Furnace, or EAF, is an even more modern method of steel production. While the common inputs for BOF steelmaking are iron ore and coal, the EAF furnace operates using scrap steel steel already produced and ready to be recycled.
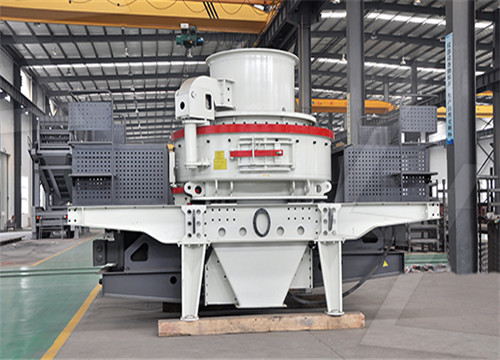
Coalsteel World Coal Association
Steel is an essential material for modern life and global steel production is dependent on coal 70% of steel produced uses coal. Metallurgical coal or coking coal is a vital ingredient in the steel making process. During the iron-making process, a blast furnace is fed with the iron ore, coke and small quantities of fluxes
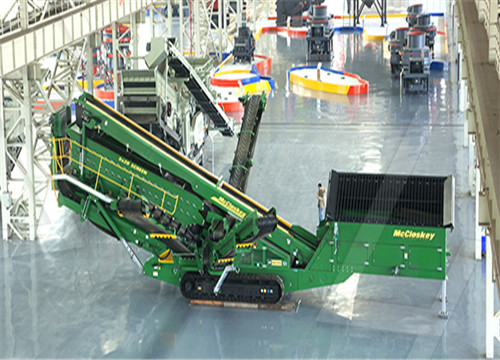
Cement Industry an overview ScienceDirect Topics
Coal is the principal source of fuel for cement kilns. Its consumption per ton of clinker largely depends on the quality and also on how effectively the cement process technology is being used. Coal consumption varies from 0.2 to 0.3 tons for every ton of clinker.
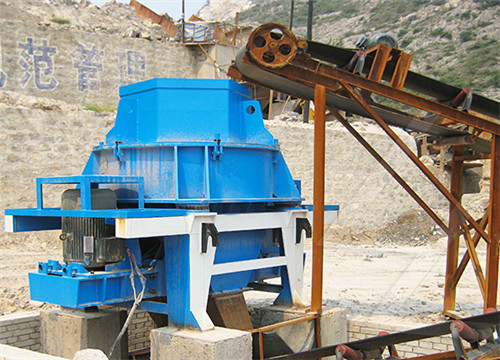
Coalsteel World Coal Association
Steel is an essential material for modern life and global steel production is dependent on coal 70% of steel produced uses coal. Metallurgical coal or coking coal is a vital ingredient in the steel making process.

Hazards Identification and Risk Assessment in Thermal
In coal crusher coal size reduced up to ¾” after that coal transfer to the boiler’s coal bunker or coal yard. In the case of emergency the coal is fetch from coal yard. Coal feeder control the quantity of coal from coal bunker and send it to the ball mill or roll mill for pulverization process. Where coal crushed to the fine powder

Fire and Explosion Prevention in Coal Pulverizing Systems
Fire and Explosion Prevention in Coal Pulverizing Systems
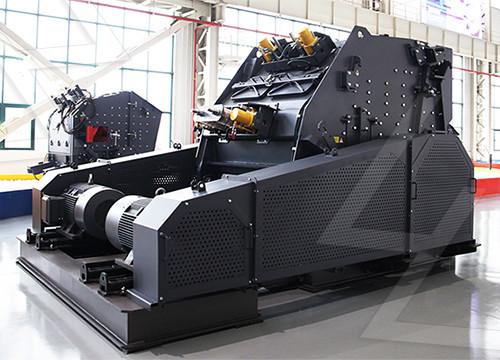
Decarbonization in steel McKinsey
2020年6月3日Steel can be produced via two main processes: either using an integrated blast furnace (BF)/basic oxygen furnace (BOF) or an electric arc furnace (EAF). While integrated players produce steel from iron ore
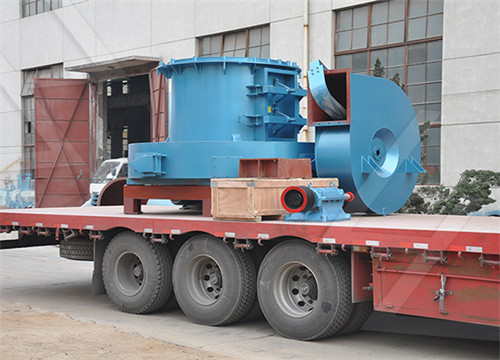
PPT Milling Process PowerPoint presentation
Today the milling drum needs not only to mill, but it is a tool to modify leather. characteristics. 3. The milling process. It is known that in the milling process, fat. liquors previously introduced in the gaps between.

Flue Gas Desulfurization (FGD) COAL HANDLING PLANTS
2021年4月11日Reagent Preparation System. The reagent preparation system of flue gas desulfurization (FGD) includes a Wet ball mill and cyclone classifiers which produce a finely ground limestone slurry at 90% solids passing through 325 mesh. One mill slurry tank and one slurry pump is supplied for one wet ball mill. The mill slurry pump will send

The Pulp and Paper Making Processes Princeton University
pulping process; collect, process, and bum lignin and waste to produce energy; and remove and treat wastes from process water for release into the environment. Steps in the Pulp and Papermaking Process Raw Material Preparation Wood received at a pulp mill may be in several different forms, depending on the pulping process
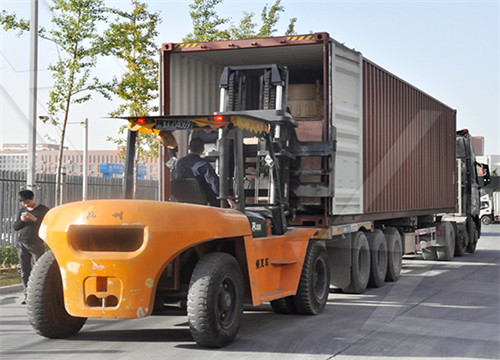
Energy audit SlideShare
2017年3月12日Energy audit 1. ENERGY AUDIT By- Assi. Prof. SHIVRAJ N NALAWADE Electrical Engineering Dept. NBNSSOE 2. Energy Audit 3. Definition of Energy Audit • As per Indian Energy Conservation Act

Coal Crushing Process Ppt caesarmachinery
milling process flow diagram ppt . Simplified Milling Process Diagram This flow diagram is In this 50-70TPH Coal crusher plant process, coal are feed to ppt recylcle crushing diagram Mining. Dec 23, 2012 coal mining flow diagram ppt process crusher. Slag Recycling; Beneficiation;
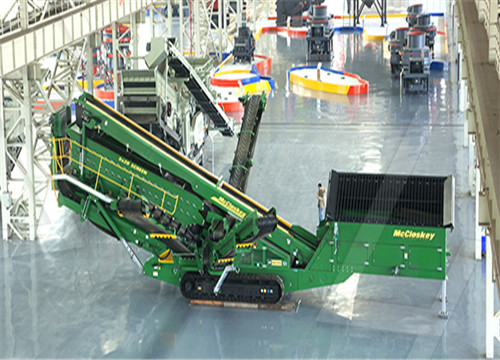
sbm/sbm clinker formation effect in coal mill ppt presentation.md
Contribute to changjiangsx/sbm development by creating an account on GitHub.

BOF and EAF Steels: What are the Differences? Economics 243
2016年3月7日The Electric Arc Furnace The Electric Arc Furnace, or EAF, is an even more modern method of steel production. While the common inputs for BOF steelmaking are iron ore and coal, the EAF furnace operates using scrap steel steel already produced and ready to be recycled.
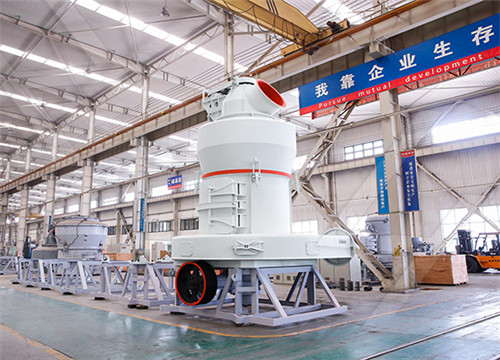
Chp Ppt Cooking Oil Making Machines Crusher Mills, Cone
ppts on power plant coal mills accidents beltconveyers.net. raymond coal mill pulverizer in thermal power plant ppt. Gulin machine in Biogas energy plant from stone oil Accidents in Refineries OECD/EU countries PPT. Chp
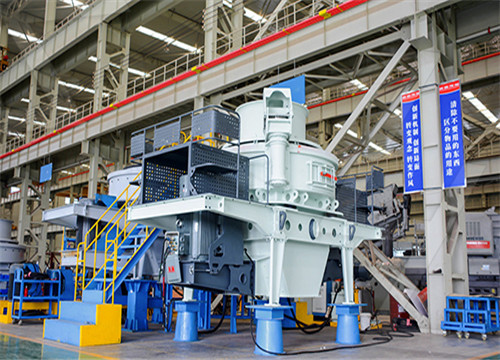
Cement Industry an overview ScienceDirect Topics
Coal is the principal source of fuel for cement kilns. Its consumption per ton of clinker largely depends on the quality and also on how effectively the cement process technology is being used. Coal consumption varies from 0.2 to 0.3 tons for every ton of clinker.