Mill To Grind Very Fine Particles Of Plastics

PolarFit® Ultra-Fine Grinding Mill Air Products
A cost-effective way to achieve ultra-fine particles. Our PolarFit® ultra-fine grinding mill is a versatile grinding system that provides a cost-effective way to reduce hard to grind materials to smaller particle sizes than can

PolarFit Ultra-Fine-Grinding Mill Air ProductsChemicals
Our new PolarFit ultra-fine-grinding mill can help you meet product specifications previously considered impossible. Although every material is different, in some cases our

Producing Fine Particles for Multiple Applications
Focus on Particle SizeSelecting A MethodThe Cryogenic AlternativeLooking Ahead
Dry milling is one of the most common methods of particle size reduction for the and rubber industries. This method uses a “roll” to compress and yield particles of different sizes so that they can be separated and sorted more easily. However, dry milling alone is not always enough to achieve the ultra-fine particle size required for more

Identifying a Pin Mill for Optimal Performance and
2018年3月21日A pin mill is one of the most commonly used impact mills for grinding bulk solid materials to medium fineness. The mill can
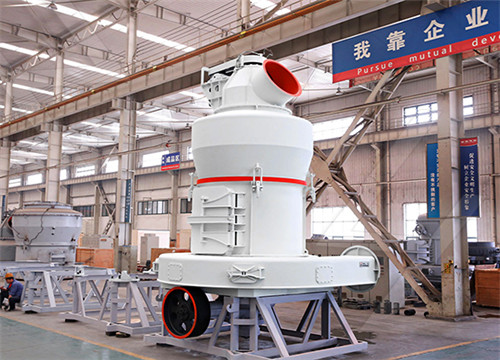
Roller mills: Precisely reducing particle size with greater
This article introduces roller mills and explains how they efficiently grind friable materials to a uniform final particle size while using relatively little energy instance, if you’re looking
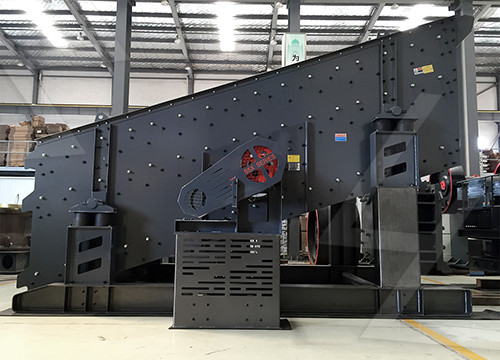
How do I make a polymer chunk into fine powder of
That is the other way we are able to make very fine powders from our polymer. We have tried ball mill but the particle size was not that low (not ~150 micron or less). Since the
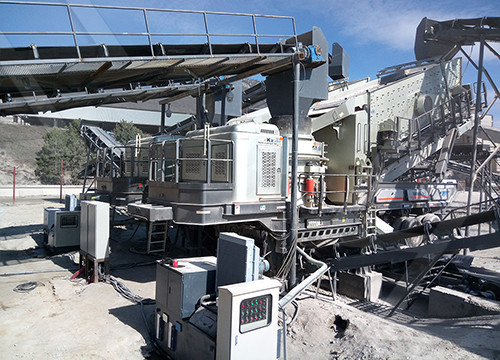
How to grind plastic ResearchGate
Depending on the size of the final particles you want to obtain there are several options you can follow. In our case we used a cutting mill (e.g., Retsch) to go down to <1 mm in particle size....
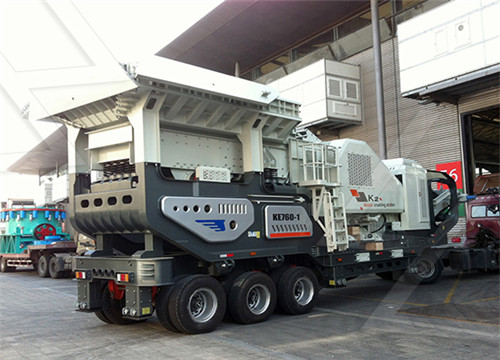
Fine grinding: How mill type affects particle shape
2017年9月1日The shape characteristics of the ore going into the plant scale ball mill and IsaMill, and coming out of the IsaMill are very similar, and these are close to the shape

Size Reduction by Grinding as an Important Stage in
Thanks to proper geometry of holes in their disks, drums or strips as well as due to appropriate relationship of the movement between neighbouring edges, multi-edge
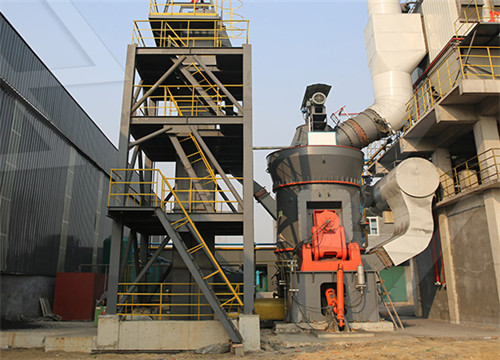
PolarFit™ Ultra-Fine-Grinding Mill Air Products
Our ultra-fine-grinding system uses the cooling power of liquid nitrogen to remove heat produced in the grinding process by controlling the temperature of your product or the mill. Key benefits include the following: • Ultra-fine particle size • More uniform particle distribution • Higher yields of particles in your target range

PolarFit® Ultra-Fine Grinding Mill Air Products
PolarFit® Ultra-Fine Grinding Mill A cost-effective way to achieve ultra-fine particles Our PolarFit® ultra-fine grinding mill is a versatile grinding system that provides a cost-effective way to reduce hard to grind
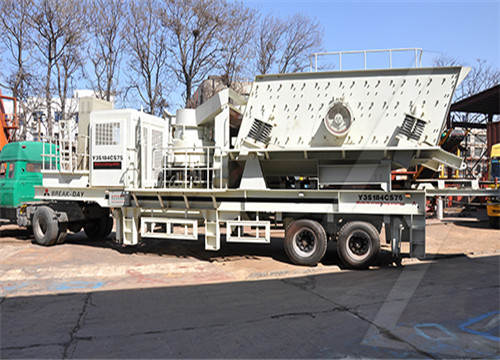
PolarFit Ultra-Fine-Grinding Mill Air ProductsChemicals
Our new PolarFit ultra-fine-grinding mill can help you meet product specifications previously considered impossible. Although every material is different, in some cases our mill can produce particles as small as 10 microns! Using the cooling power of liquid nitrogen and multiple impact mechanisms, our mill can help you achieve:

Process engineering: Particle size reduction techniques and
2005年2月15日Air aspiration is often used, especially in jet mills, to remove fine particles by entrainment while retaining larger particles. Hammer, ball and rod mills frequently have screens on their discharge to retain large particles and media while passing fine particles.

Fine grinding: How mill type affects particle shape characteristics
2017年9月1日The shape characteristics of the ore going into the plant scale ball mill and IsaMill, and coming out of the IsaMill are very similar, and these are close to the shape characteristics of particles in the laboratory feed, as well as progeny from the laboratory stirred mill. Although fine and ultra-fine grinding in the laboratory ball mill led to
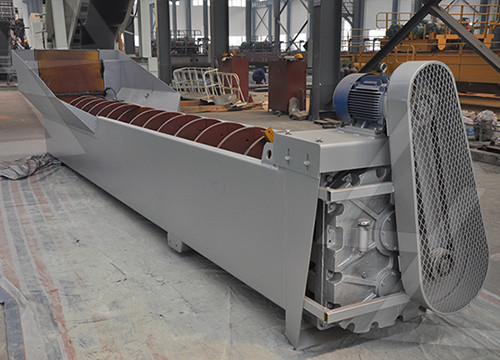
mill to grind very fine particles of
Coarse and Fine Particle Flotation Recovery. Jun 02, 2016 In several gold mills nearly 50% of the gold content of the ore is recovered in a higher grade concentrate by the introduction of a Unit Cell between the grinding mill and classifier. facility with which coarse particles float and of the greater liberation of fine particles, are presented in the diagrammatic

Value adding limestone to filler grade through an ultra-fine grinding
In this study, ultra-fine grinding of limestone was carried out in jet mill using four levels of classifier rotational speed and grinding pressure. The holdup amount was determined during the grinding process, while the feed rate was kept constant at 8 kg/h. The ground product was characterized for its particle size and shape.
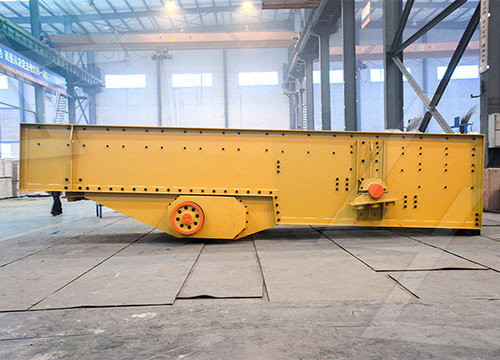
The Best Countertop Grain Mills and Flour Grinders
2020年1月2日NutriMill Classic 760200 High Speed Grain Mill, available on Amazon. The stainless steel impact heads can be adjusted to produce coarse meal through to super fine for cakes and pastries. And with
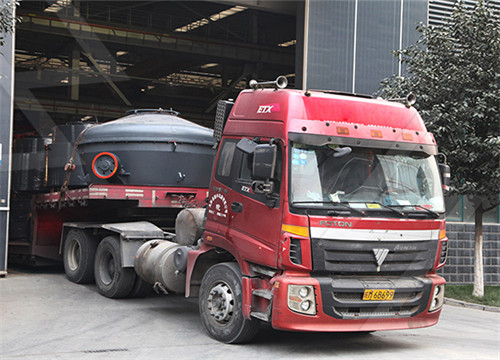
Grinding Mill an overview ScienceDirect Topics
There is also a separate type of mills producing very fine coal powder, called micronizing mills. Macerators accomplish the chopping action effectively that can reduce the creation of and rags collecting on downstream equipment. believed that the mechanism of breakage of particles in a grinding mill was analogous to the slow
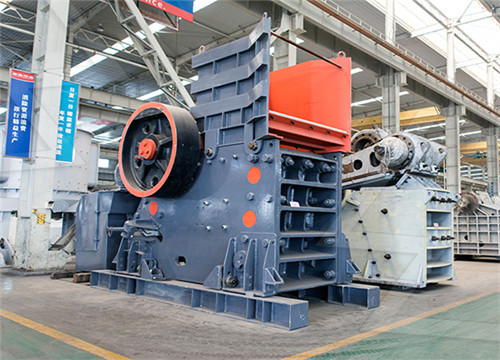
Energy-Dependent Particle Size Distribution Models for Multi-Disc Mill
Grinding is an important element in the processing of biological materials, such as cereal grains, y biomass, waste, etc., and its purpose is to reduce bulk density and storage areas, improve nutrient release, prepare for further processing, etc. [1,2,3,4,5,6].In production processes, e.g., production or pellet manufacturing processes, the

Analysis of grinding in a spiral jet mill. Part 1: Batch grinding
2020年11月1日Part 2: Semi-batch grinding. The breakage and classification of particles in a spiral air jet mill, operated in a semi-batch mode, is studied for varying operating conditions. The particle size

Planetary Ball Mill PM 400 RETSCH powerful and quick grinding
To produce very fine particles of 100 nm or less (nano-scale grinding) by wet grinding, friction rather than impact is required. This is achieved by using a large number of small grinding balls which have a large surface and many friction points. The ideal filling level of the jar should consist of 60 % small grinding balls.

CEMENT SikaGrind® FOR VERTICAL ROLLER MILLS
A high content of very fine particles on the grinding track usu-ally troubles the stability of the grinding bed. Fine particles lower the interparticle friction, which reduces the grinding efficiency. Fines on the grinding table cause struggle with the compaction and de-aeration, resulting in vibration and higher wear of the equipment.

PolarFit Ultra-Fine-Grinding Mill Air ProductsChemicals
Our new PolarFit ultra-fine-grinding mill can help you meet product specifications previously considered impossible. Although every material is different, in some cases our mill can produce particles as small as 10 microns! Using the cooling power of liquid nitrogen and multiple impact mechanisms, our mill can help you achieve:

Planetary Ball Mill PM 400 RETSCH powerful and
To produce very fine particles of 100 nm or less (nano-scale grinding) by wet grinding, friction rather than impact is required. This is achieved by using a large number of small grinding balls which have a large surface
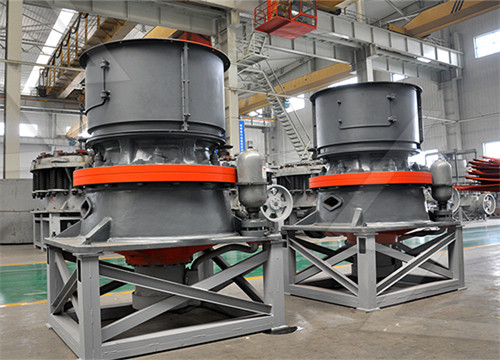
Fine grinding: How mill type affects particle shape characteristics
2017年9月1日The shape characteristics of the ore going into the plant scale ball mill and IsaMill, and coming out of the IsaMill are very similar, and these are close to the shape characteristics of particles in the laboratory feed, as well as progeny from the laboratory stirred mill. Although fine and ultra-fine grinding in the laboratory ball mill led to
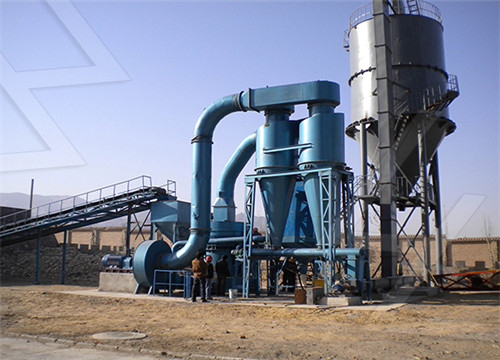
Optimization of some parameters of stirred mill for ultra-fine grinding
2011年3月10日The fine particles present/produced during grinding cause high pulp viscosity and reduce the grinding performance, especially in the case of pulp density that exceeds 75% by weight [26], [27]. To avoid negative effect of high viscosity caused by very fine particles, various type of grinding aids such as polymeric chemicals are added to

Analysis of grinding in a spiral jet mill. Part 1: Batch grinding
2020年11月1日The breakage and classification of particles in a spiral air jet mill, operated in a semi-batch mode, is studied for varying operating conditions. The particle size distributions of the product...

The Best Countertop Grain Mills and Flour Grinders
2020年1月2日NutriMill Classic 760200 High Speed Grain Mill, available on Amazon. The stainless steel impact heads can be adjusted to produce coarse meal through to super fine for cakes and pastries. And with
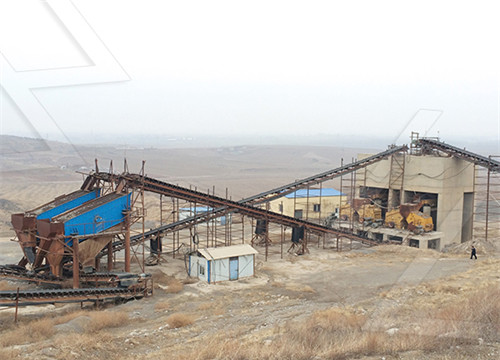
Value adding limestone to filler grade through an ultra-fine grinding
In this study, ultra-fine grinding of limestone was carried out in jet mill using four levels of classifier rotational speed and grinding pressure. The holdup amount was determined during the grinding process, while the feed rate was kept constant at 8 kg/h. The ground product was characterized for its particle size and shape.
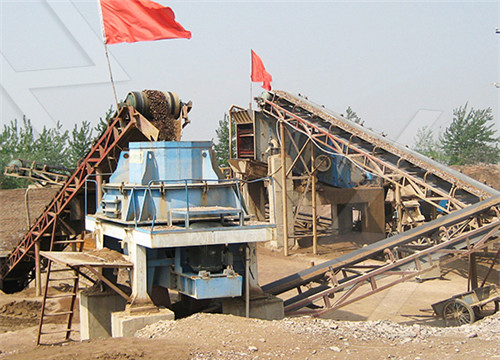
equipment used to grinding to very fine particles
英语网站资料. Contribute to sbmboy/en development by creating an account on GitHub.
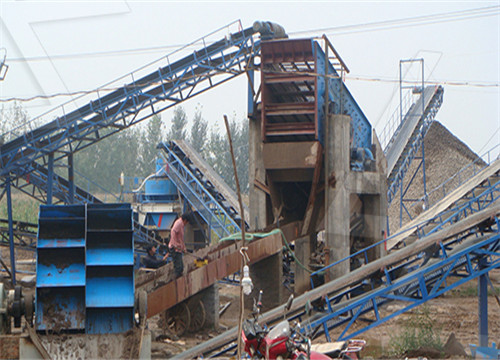
Energy-Dependent Particle Size Distribution Models for Multi-Disc Mill
Grinding is an important element in the processing of biological materials, such as cereal grains, y biomass, waste, etc., and its purpose is to reduce bulk density and storage areas, improve nutrient release, prepare for further processing, etc. [1,2,3,4,5,6].In production processes, e.g., production or pellet manufacturing processes, the

CEMENT SikaGrind® FOR VERTICAL ROLLER MILLS
A high content of very fine particles on the grinding track usu-ally troubles the stability of the grinding bed. Fine particles lower the interparticle friction, which reduces the grinding efficiency. Fines on the grinding table cause struggle with the compaction and de-aeration, resulting in vibration and higher wear of the equipment.
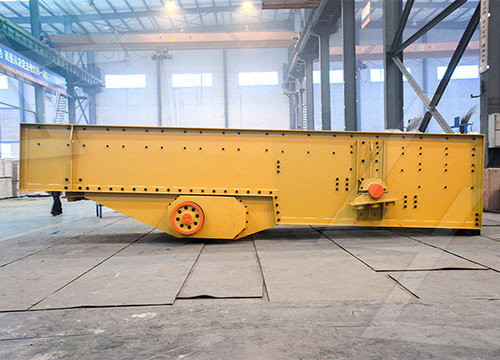
STM MICROTEC on LinkedIn: #cryogenic #grinding #tire #rubber
Do you want to discover the benefits of #cryogenic #grinding for recycling #tire and #rubber? STM Microtec offers the MPC400 CRYO Peg Mill Cryogenic
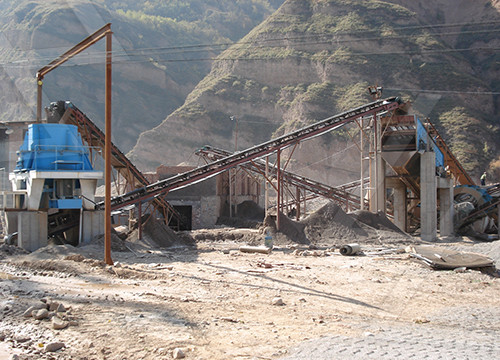
Picture: Loesche GmbH, Germany CEMENT SikaGrind® FOR
In a ball mill, the particles are ground by repeated impact forces. The material needs usually more than 20 minutes from mill entrance to outlet, uncountable impacts take place on this way. Depending on the efficiency of the separator and the Grinding Aid, agglomerates of fine particles are rejected and pass the ball mill again.

Plastic ManufacturingFRP Dust Collection RoboVent
The industry encompasses a broad range of processes, from pelletizing and conveying to molding and grinding. Along the way, a lot of plastic dust is created. Controlling this dust (called “fines”) is essential to protect the health of workers and prevent dangerous explosions from charged, combustible plastic dust.